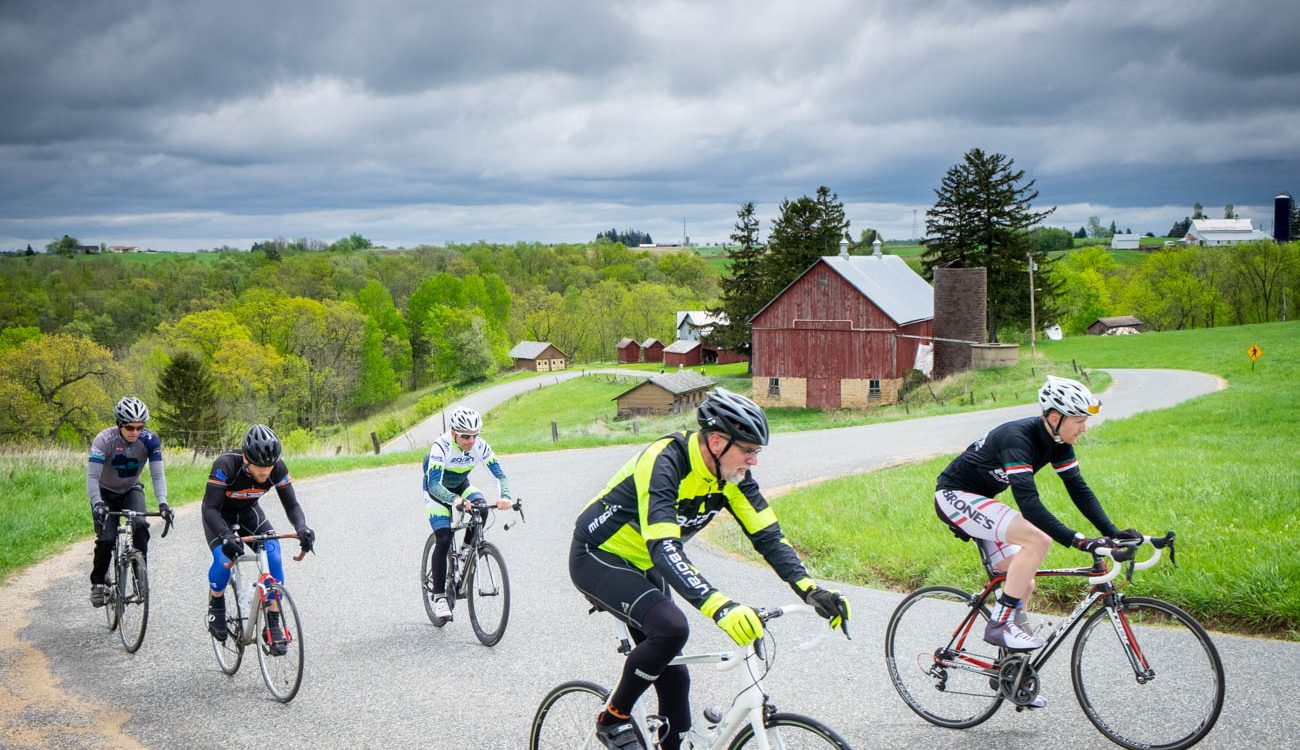
Borah Teamwear
A Wisconsin bike industry leader nestled in the heart of Wisconsin’s picturesque Driftless Region.
After joining an employee ride that included two 19 percenters in our ten-mile loop, my Milwaukee co-worker Dave Schlabowske, joked that he was looking at the Borah Teamwear website jobs page and checking real estate prices in Coon Valley.
We counted two cars on our lunch hour ride outside the quaint little town, 16 miles southeast of my hometown of La Crosse. No cars, killer climbs, eye-tearing descents, gorgeous scenery, and the home to one of our state’s bicycle industry stand-outs; I can see why Dave was thinking about moving!
With a population of just 776, Coon Valley may be some of the prettiest, and toughest riding in Wisconsin. With state-of-the-art production technologies, the 35 employees at Borah Teamwear pump out about 10,000 made in Wisconsin garments a month!
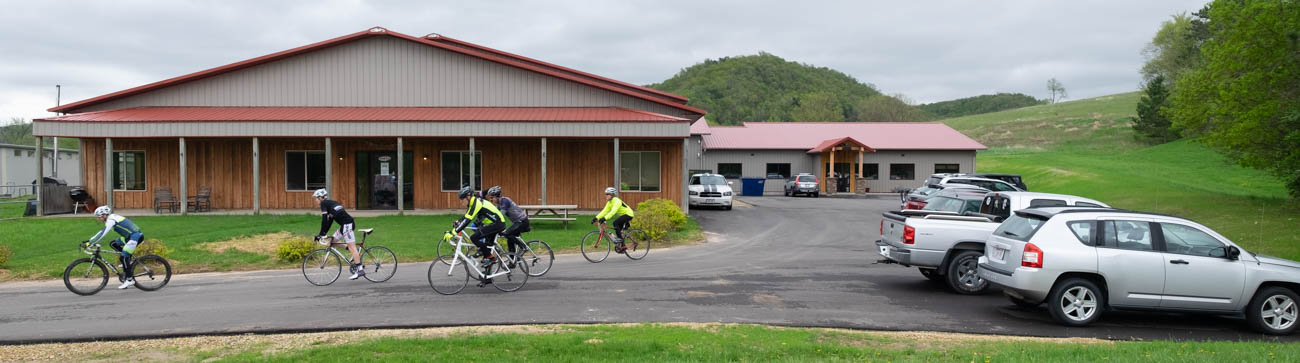
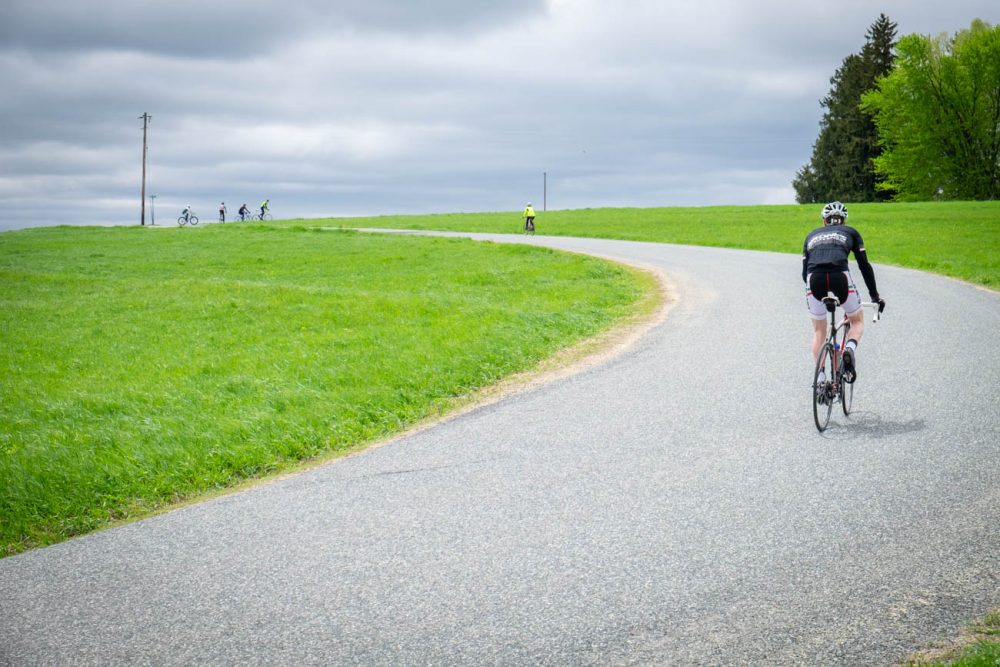
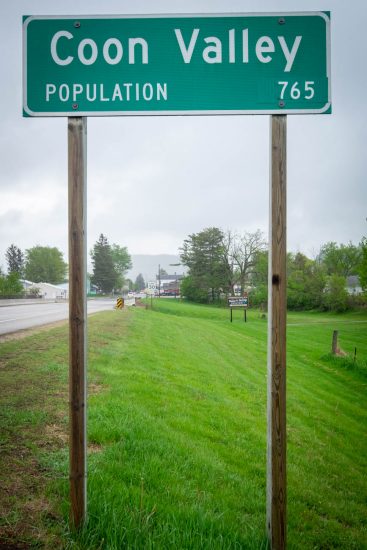
Nestled in the heart of Wisconsin’s picturesque Driftless Region, Borah Teamwear was started by Chris Jackson, an avid bike racer and skier. Borah Teamwear’s story began in 1996 when Chris saw a growing demand for well-made, high-functioning mountain bike shorts. He decided to make a pair, and called his prototype the Sawtooth ATB Short. At the time, Chris was an independent sales rep in the bike industry, selling to cycling stores in the midwest. With a great first product in hand and some hard work, Chris sold 300 pairs of shorts in year one. Not much later, Borah Teamwear was selling thousands of shorts, jerseys, and cycling gear all over the USA.
Always looking to fill a niche, the folks at Mt. Borah began to think about offering custom bicycle apparel. Digital dye sublimation was just coming into the marketplace and Borah was one of the first to utilize the technology within the cycling and ski industries. By doing so, Borah was able to offer low minimum orders, fast turnaround times, and unlimited color selections. This made it possible for small teams, clubs and organizations to order small quantities for less money and receive the product within a reasonable time frame.
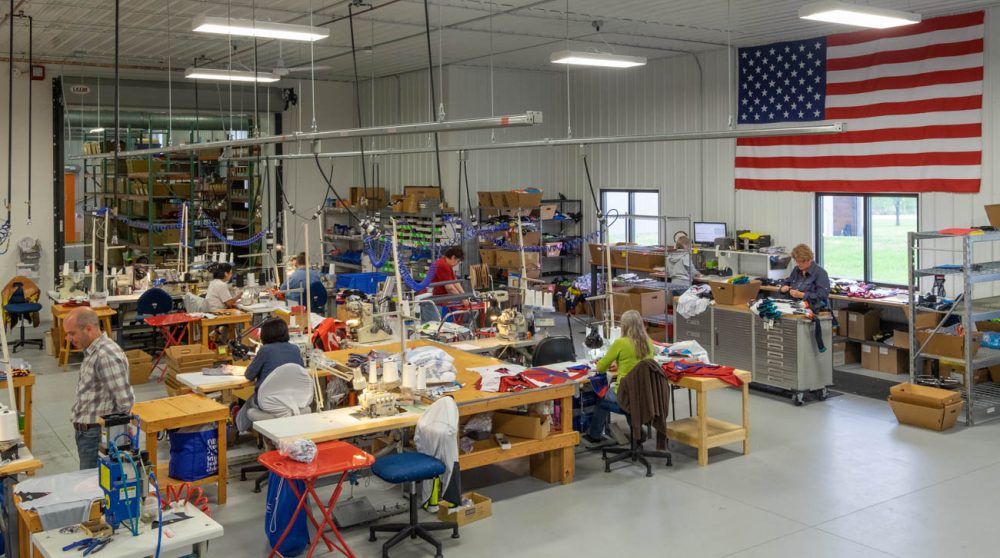
Handmade to order, right here in Wisconsin. Sublimation printers are the name of the game.
While other companies moved production overseas and grew exponentially, Chris and the crew at Borah Teamwear have stuck to their Wisconsin roots. Growth has been steady and a result of offering quality products, made in the USA, quick turnaround times and small minimums. You can find slightly less expensive kits, but you won’t find better service anywhere.
Dave and I were greeted by a nice “Welcome Wisconsin Bike Fed” sign in the entryway of their recently expanded building, but what really made us feel at home was the aroma of freshly brewed coffee and a bunch of cool bikes parked outside people’s work spaces. Dave bounced from top of the line Trek carbon rigs to custom fillet brazed made by a small Wisconsin frame builder.
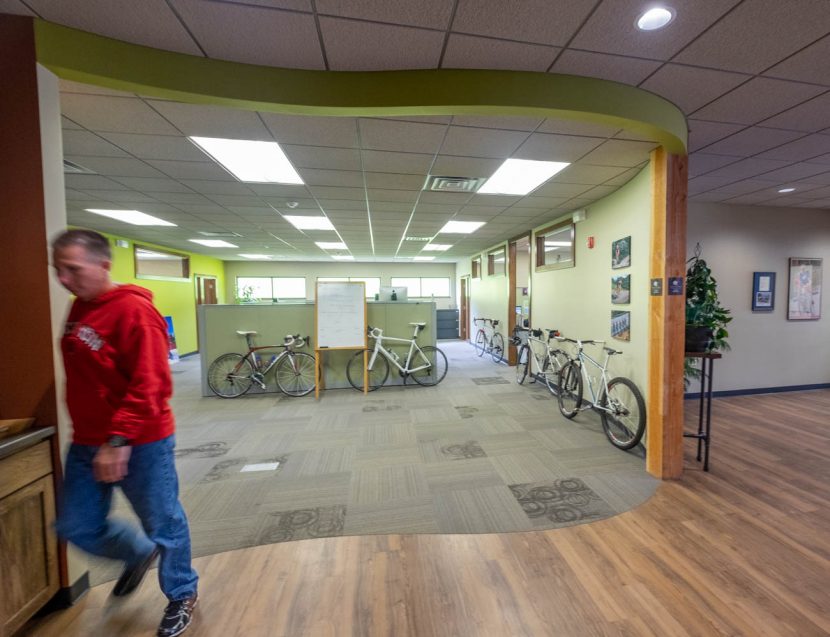
Borah presents their complete line of clothing on display hanging in the lobby next to a huge table made from a local tree. I highly suggest your team make a personal pilgrimage to see where your kits are produced, and take the opportunity to try on the full line of gear that Mt. Boarah manufactures.There is no better way to make decisions than to see and feel the choices available. Something new that you might want to consider is their ultralight jacket. With an inside stuff pocket, the ultralight jacket packs into the palm of your hand and with street good looks, the lightest garment Team Borah makes might also be the most versatile.
The new office space is home to their employees who work on design, customer service, marketing and development. The new building nearly doubled Mt Borah’s manufacturing space, adding 9,000 sq ft, giving all the seamstresses and other workers more elbow room.
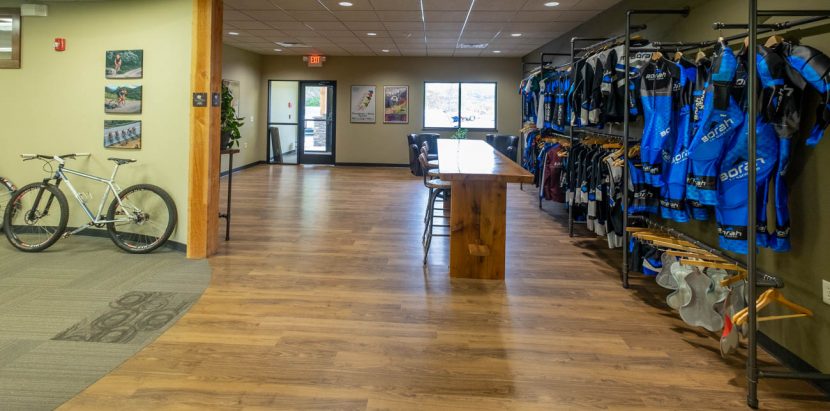
The print room is climate controlled, specific to the ink, paper, and heat applied to the fabric. All steps in the process are monitored closely to ensure the images come out crisp, clean and color true. The sublimation transfer process uses large rolls of fabric, ink, paper, and heat. Everything goes in together and the heat and pressure transfer the ink onto the fabric, the paper is then peeled off (and recycled) and the printed fabric comes out on enormous rolls.
Next the rolls of sublimated fabric head over to the new Gerber cutter, a laser guided machine which cuts a jersey in about ten seconds. That all used to be done by hand, so the machine adds tremendous efficiency helping Borah compete with companies that do production overseas where labor and environmental costs are lower. The addition of the technology has improved efficiency without replacing any employees.
The 35 full-time employees include seamstresses, technicians, customer care, graphic artists, and Chris. Everyone is from the general area, and they can all feel proud to be part of a growing company that produces products that are 100% custom-made, hand-sewn and manufactured in the Coon Valley, WI USA. I certainly feel that way when I put on my Mt Borah Bike Fed kit.
Many of the Borah Teamwear employees are “test pilots” who get to try out what they make when out skiing, running and riding. Ben Wizner, Marketing Director, has even organized Borah Teamwear’s own commuting challenge that began in May and will continue through October 15th. Their employees ride in to work from Wesby, Viroqua, and La Crosse and can earn prizes for a variety of categories: total miles, total commutes, fastest commutes, longest commutes, and most commutes in one week
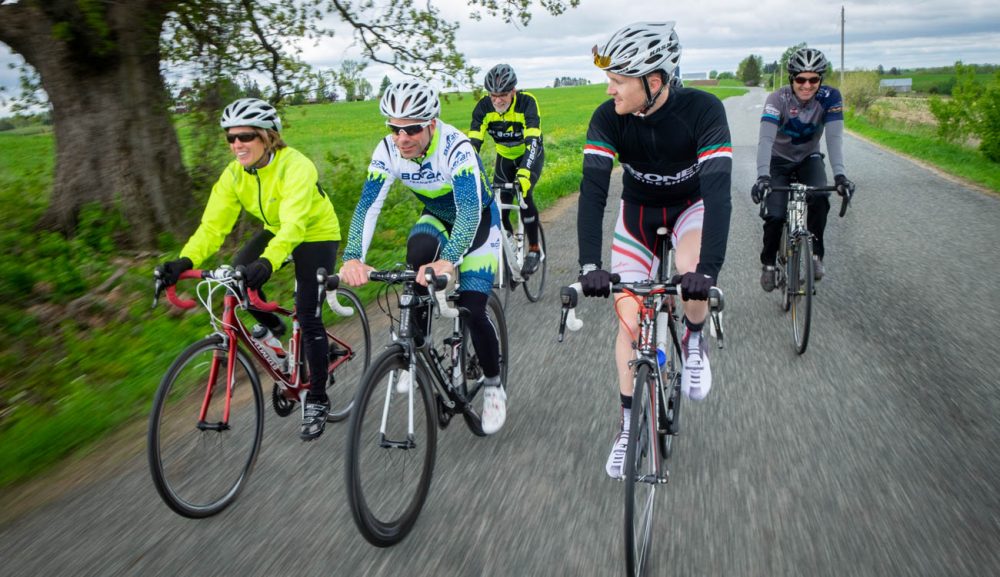
The company has changing rooms and showers to make clean up convenient when arriving at work. Clinton Grabhorn, Graphic Designer, enjoys his sunrise commute recommending his early ride as a great way to get the day started. Of course, I encouraged Ben to utilize our Wisconsin Bike Challenge to track miles as well.
As mentioned at the start of this story, we finished our facility tour with a ride. Directly out the front door of Borah Teamwear is Mill Road which becomes Sveum Ridge Road. It starts in the valley and climbs up onto a ridge with a 19% grade. On a 45 degree rainy day in May, the sun peaked out briefly just as we hit the top of the ridge, rewarding us for our climb. As we crested the ridge, were bathed in warm sunshine as dark cloud hung over a wonderful old farm on the horizon, a spectacular view that just screamed bicycling in Wisconsin.
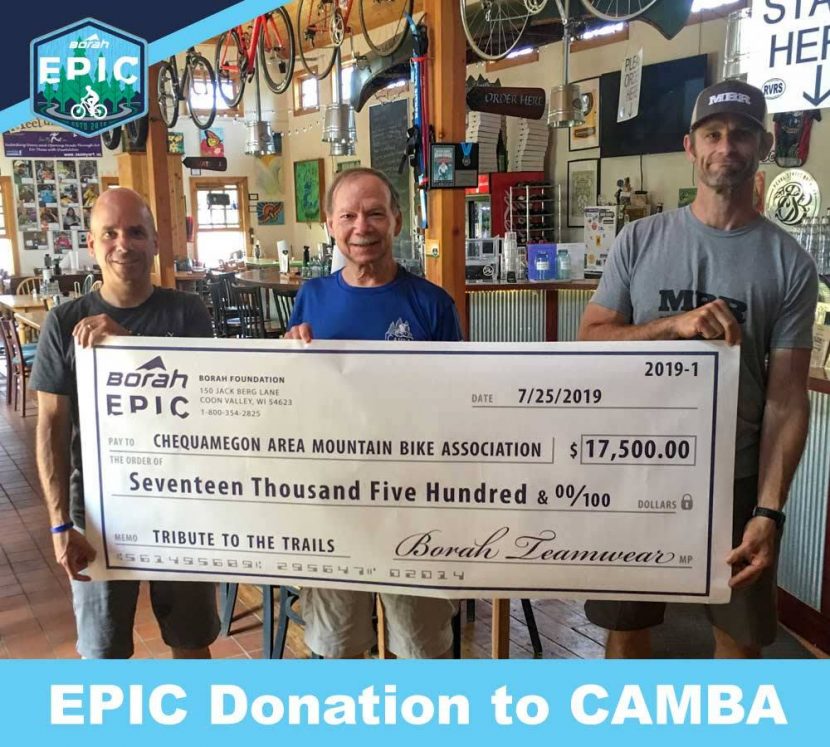
As we pedaled on together, we descended onto Spring Coulee Road passing over burbling, crystal clear trout-filled stream. We stopped for a few minutes to regroup, admire the view and share grins after the rocket-like descent. The only things missing were motor vehicles, and their absence only added to the treasure of the town roads in Vernon County. Thanks to the crew at Borah Teamwear for supporting the Bike Fed, for their support of Chequamegon Area Mountain Bike Trails with the Mt Borah Epic. The Borah Epic held its seventh annual event this past June and welcomed a record number of riders in the half, full and new gravel race distances. For year seven, the Epic generated a $17,500.00 donation to benefit the CAMBA trails, which now totals $107,000 since the race was founded in 2013!
And thanks letting us join your lunchtime routine to remind us what a special place Wisconsin is to ride a bike.