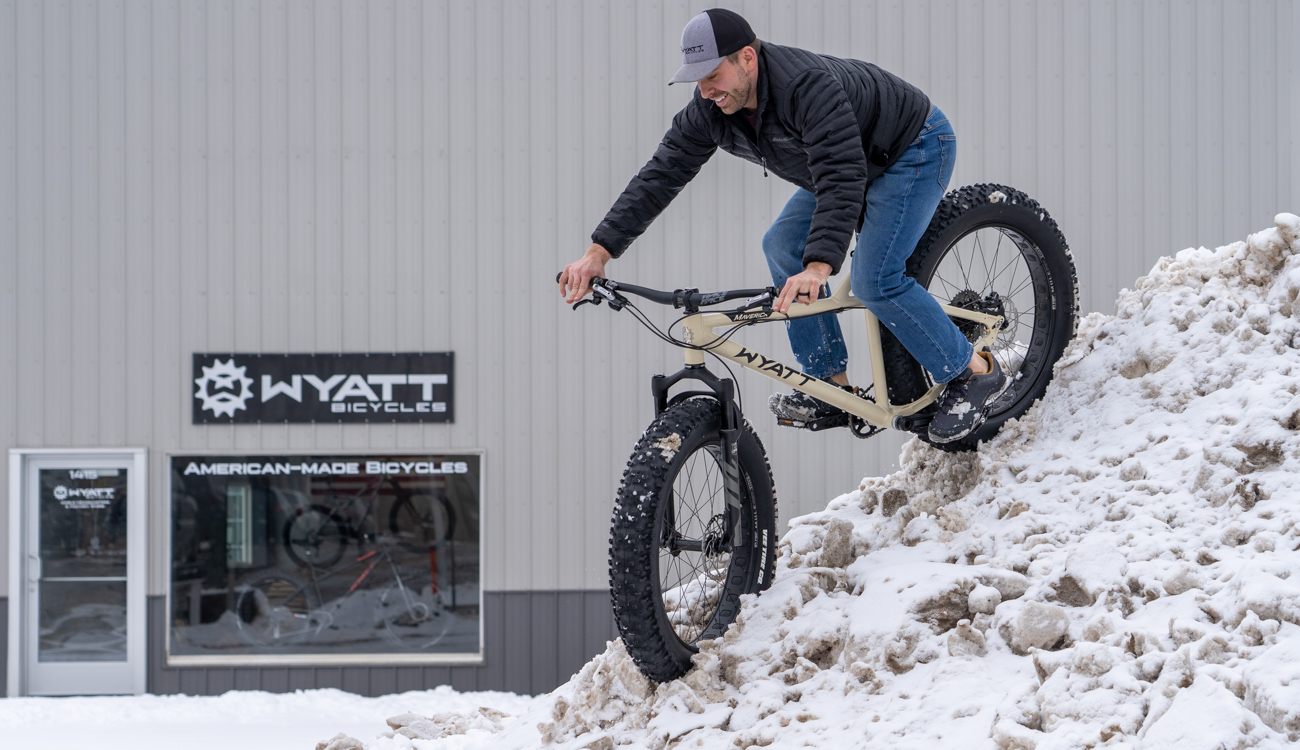
Wyatt Bicycles
Proudly supporting Wisconsin manufacturing.
I always wanted to support American manufacturing. My dream was to start manufacturing bicycles in the U.S.
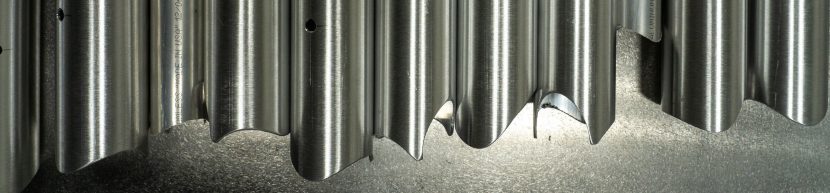
As a mechanic for the Green Bikes Program at the Rec Sports Department at the University of Wisconsin, La Crosse, Wyatt Hrudka was frustrated by the constant inflow of derailleur adjustments. The Green Bike program rents donated used bicycles to UW La Crosse students for $15 a semester. Hrudka thought students would be better served by inexpensive single speed bicycles that didn’t need so much regular maintenance.
Enrolled as an information systems major, he also really enjoyed the business classes he was taking.
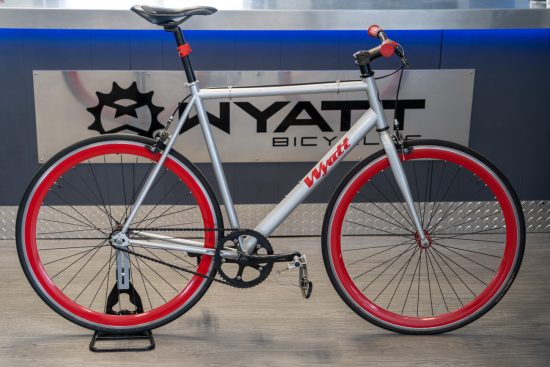
“What sparked my business side was that I saw a lot of students riding around campus with their gears constantly grinding. It was the most common problem. I thought single speed bikes would be the solution, so I did some market research on it. I was really enjoying my business classes, so I wrote a business plan and reached out to factories in China to keep the costs of the bikes down. I sent them my designs and a factory I liked sent me some prototypes. The next step was to find funding to order a container full.”
Not surprisingly, the banks all said no to a college student starting a new bike company. Undeterred, Hrudka was able to get funding from his family, sell out his first container and pay back the loan. His next product was a fat bike, the Driftless model, which he designed and had made at the same factory in China that was making his single speed commuter bikes.
“I did that for a couple years. What really set us apart from other companies was our online customization program. That was kind of unique back then. We got the bare frames and did all our powder coating at a local La Crosse company, customers could choose from a lot of colors, pick the different components and we would build them up here and ship them direct.”
That is a very different model from most major brands who only have a couple colors and a few build specs for each model because all that is done overseas. While Wyatt Bicycles found reasonable success with that model for a couple years, he always cared about U.S. manufacturing.
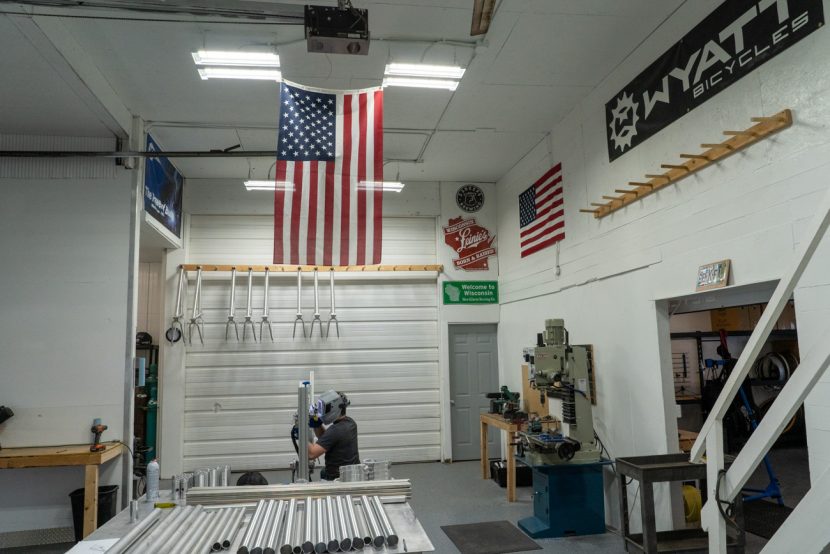
USA made aluminum bars are converted into bicycle frame components with the CNC machines in Wehrs Machine Shop. Wyatt and Jesse Bjorkman discuss mitering tubing in bulk using the CNC machines as a way to increase manufacturing efficiencies.
“I always wanted to support American manufacturing. My dream was to start manufacturing bicycles in the U.S. One of the things that triggered it was the factory I was working with was starting to sell my designs to other companies. Then in 2017 I saw one of the bike frames I designed advertised on their website under a different private label brand. I said I was done with China and started looking into what I would need to build my bikes here.”
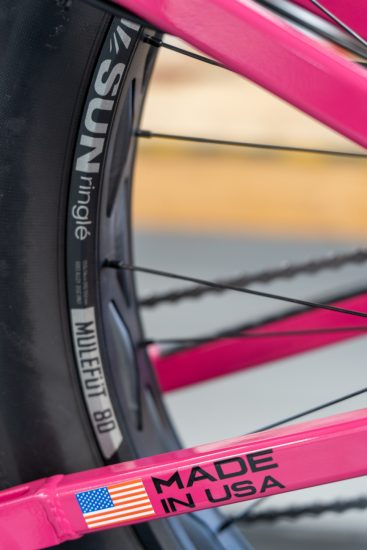
One of Wyatt Bicycles early customer was Chad Wehrs, of Wehrs Machine & Racing Products in nearby Bangor, WI. Wehrs manufactures automobile racing parts and offered that if Wyatt ever needed anything machined, they would be interested in helping.
“Well, I reached out to Chad in 2017 and said I was considering manufacturing my bikes in the USA. They started out just doing my dropouts, then I talked to Chad’s welder, Jesse Bjorkman. He came by and did a really great job welding the prototype frames.”
Bjorkman welded frames in the evenings and on weekends for Wyatt for a little more than a year, but it was limiting. There was no way Wyatt Bikes could scale up with that arrangement so Wehrs Machine formally partnered with Wyatt. Wyatt Bicycles even moved his shop from La Crosse to a building in Bangor owned by Wehrs.
Wehrs now orders all the American made aluminum, machines the parts and welds the frames. It takes about seven hours to build and fully assemble a bike, with two to three hours for machining and welding. After the bikes are welded, they are shipped across the Mississippi River for heat treating at a nearby company in Minnesota, then shipped back for a final alignment by Wyatt before they are powder coated at Left Coast Powder Coating, in La Crosse. The owner of Left Coast, Josh Twitchell, was also an early investor in Wyatt Bicycles. Finally the bikes return to Wyatt for assembly and shipping.
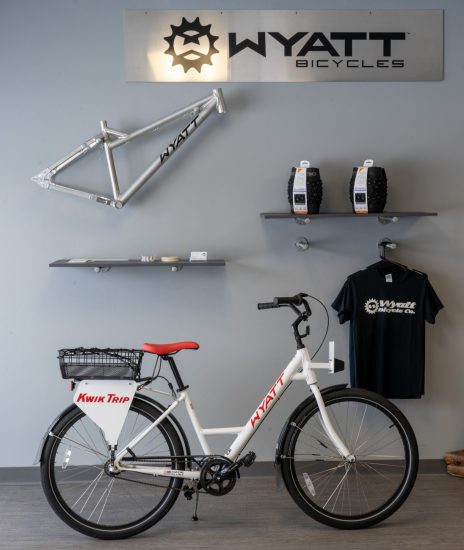
The close working partnership with Wehrs is key to keeping the price point competitive. They are also looking at some additional manufacturing efficiencies that could happen with CNC or laser mitering of the tubes. With starting prices for a complete bike just above $2,000, Wyatt Bikes are an easy choice for anyone looking for an American made fat bike or mountain bike.
Interestingly, if you search the internet for Made in USA fat bike, Wyatt’s unassuming company pops up at the top of the search results. That is in part because there are not many fat bikes made in the United States outside of independent frame builders. The other reason is Hrudka continues to make good use of his information systems degree maximizing his website’s SEO. He does do some private consulting on web design and SEO for those who like to hire from within our cycling community.
If you are interested in test riding a Wyatt, you can find the bikes at Everyday Cycles in Milwaukee and Stache Bike and Adventure in Eau Claire, and, of course, at Wyatt Bikes in Bangor.